Początek: od koncepcji do projektu
Tworzenie maszyn przemysłowych zaczyna się od precyzyjnie określonej potrzeby. Może to być optymalizacja istniejącego procesu, wprowadzenie nowej technologii lub zastąpienie manualnych operacji automatyzacją. Kluczowym krokiem jest analiza wymagań klienta – określenie funkcji maszyny, jej wydajności, środowiska pracy oraz budżetu. To etap, w którym inżynierowie współpracują z ekspertami ds. produkcji i użytkownikami końcowymi, by zrozumieć specyfikę branży i potrzeby operacyjne.
Po sformułowaniu wymagań powstaje wstępna koncepcja. W tym momencie definiuje się wymiary, główne elementy oraz zastosowane technologie, takie jak pneumatyka, hydraulika czy robotyka. Kluczowe jest wykonanie analizy wykonalności, czyli weryfikacji, czy założenia są technicznie i ekonomicznie realne.
2. Projektowanie i symulacje
Właściwy proces projektowania opiera się na specjalistycznym oprogramowaniu CAD (Computer-Aided Design). Na tym etapie inżynierowie tworzą szczegółowe modele 3D maszyny, które uwzględniają wszystkie elementy mechaniczne, elektroniczne i automatyki. Projekt 3D pozwala zweryfikować poprawność konstrukcji jeszcze przed produkcją fizycznych prototypów, co znacznie obniża ryzyko błędów.
Równolegle przeprowadzane są symulacje komputerowe. Testowane są m.in. wytrzymałość materiałów, efektywność mechanizmów i zgodność z normami bezpieczeństwa. Dzięki temu można ocenić, jak maszyna zachowa się w rzeczywistych warunkach pracy. Zaawansowane narzędzia symulacyjne pozwalają również optymalizować zużycie energii czy wydajność produkcyjną.
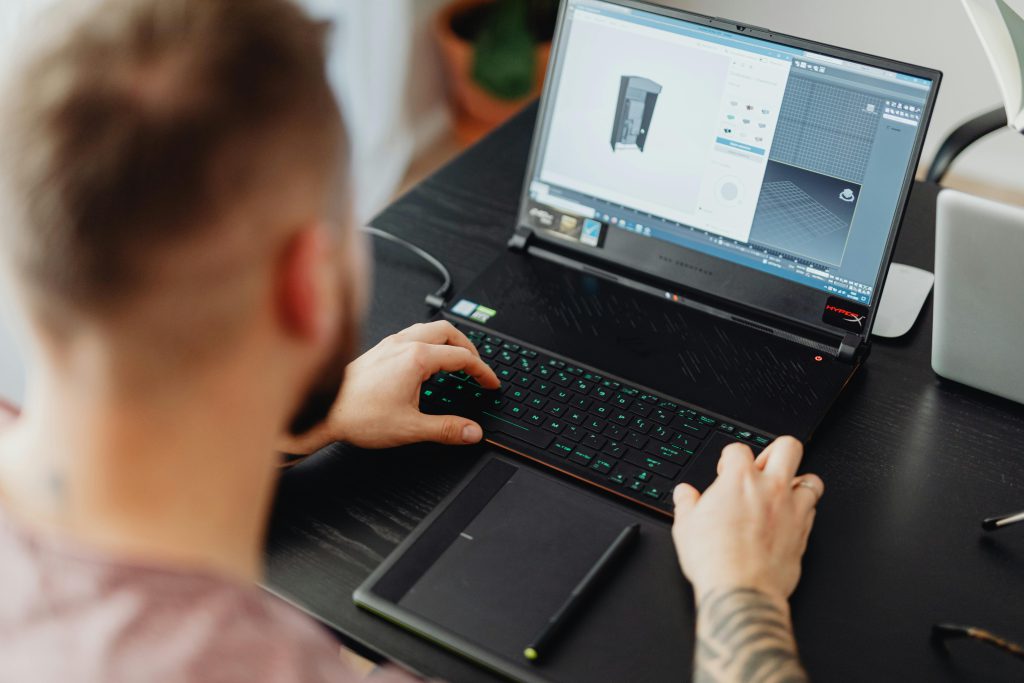
3. Budowa prototypu i testowanie
Po zaakceptowaniu projektu rozpoczyna się budowa prototypu. To najważniejszy etap, ponieważ pozwala przekształcić teorię w rzeczywistość.
- Prototyp to pierwsza fizyczna wersja maszyny, która przechodzi szereg testów. Sprawdzane są m.in. precyzja działania, trwałość oraz funkcjonalność zgodna z założeniami.
- Testy mogą ujawnić nieoczekiwane problemy, takie jak wibracje, niewystarczająca wydajność czy trudności w obsłudze. Na tym etapie często wprowadza się korekty – od drobnych zmian w konstrukcji po modyfikacje oprogramowania sterującego.
- Ważnym aspektem jest także ergonomia, aby maszyna była intuicyjna w obsłudze.
4. Produkcja i wdrożenie
Po zakończeniu testów i ostatecznej akceptacji prototypu rozpoczyna się produkcja seryjna. Proces ten wymaga precyzyjnej organizacji, zwłaszcza gdy maszyna składa się z setek komponentów. Kluczowe jest zapewnienie jakości na każdym etapie montażu oraz przeprowadzanie testów funkcjonalnych dla każdego wyprodukowanego egzemplarza.
Wdrożenie maszyny w zakładzie produkcyjnym klienta to kolejny krok. Inżynierowie przeprowadzają instalację, konfigurację i szkolenie operatorów. Często wdrażane są systemy monitorowania pracy maszyn w czasie rzeczywistym, co umożliwia ich zdalną diagnostykę i optymalizację.
5. Utrzymanie i rozwój
Nawet po zakończeniu wdrożenia praca nad maszyną się nie kończy. Kluczowe jest zapewnienie serwisu posprzedażowego – regularne przeglądy, modernizacje i szybkie usuwanie usterek. Dzięki nowoczesnym systemom IoT (Internet of Things) możliwe jest monitorowanie parametrów maszyny zdalnie i przewidywanie potencjalnych awarii.
W odpowiedzi na zmieniające się potrzeby rynku oraz klientów, często rozwija się kolejne wersje maszyny. Nowe modele mogą oferować lepszą wydajność, niższe zużycie energii lub większą elastyczność w dostosowywaniu do różnych procesów.
Podsumowanie
Proces tworzenia maszyn przemysłowych to skomplikowana, ale fascynująca droga – od idei po gotowy produkt pracujący na liniach produkcyjnych. Sukces wymaga ścisłej współpracy interdyscyplinarnej, zaawansowanych technologii i ciągłego doskonalenia.